-
-
Are you considering automating your pouch packaging with rollstock?
Then this guide is for you!
At EcoPackables, we’re committed to helping you explore all your sustainable packaging options. This guide covers everything you need to know when transitioning to rollstock packaging.
IN THIS GUIDE
- What is Rollstock
- Industries That Benefit from Rollstock Packaging
- Sealing Methods in Rollstock Packaging
- Rollstock Material Options, Barrier Considerations and Customization
- Is Rollstock Right for Your Business?
What is Rollstock?
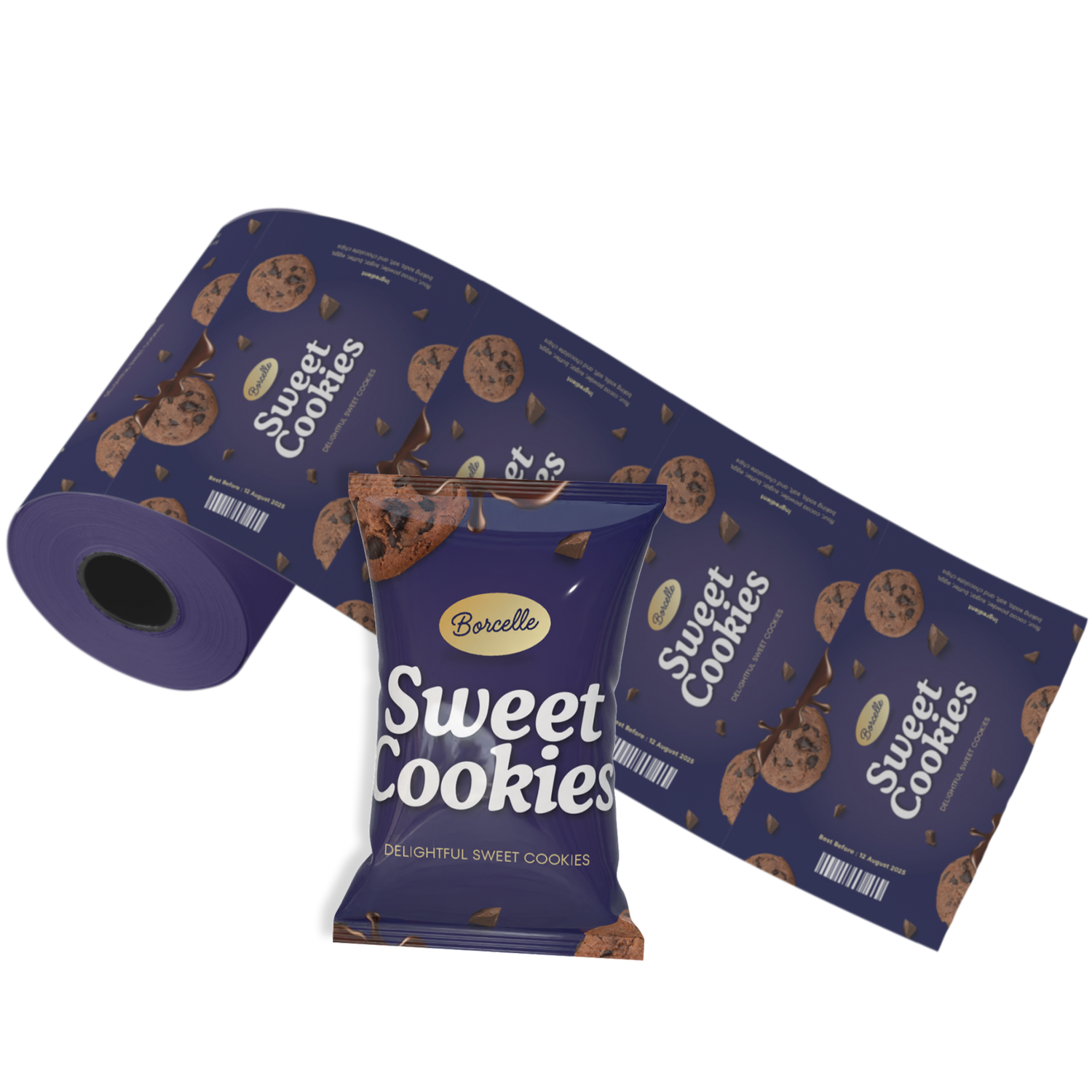
Rollstock refers to continuous rolls of flexible packaging materials, such as plastic, paper, foil, or laminates, used in form-fill-seal (FFS) machines to create pouches or bags. Instead of using pre-made pouches, rollstock allows packaging to be formed, filled, and sealed in one streamlined process, making it a cost-efficient and high-speed solution for large-scale production. Rollstock also allows for customization, meaning brands can integrate features like zippers, resealable closures, and high-barrier films to enhance product protection and consumer convenience.
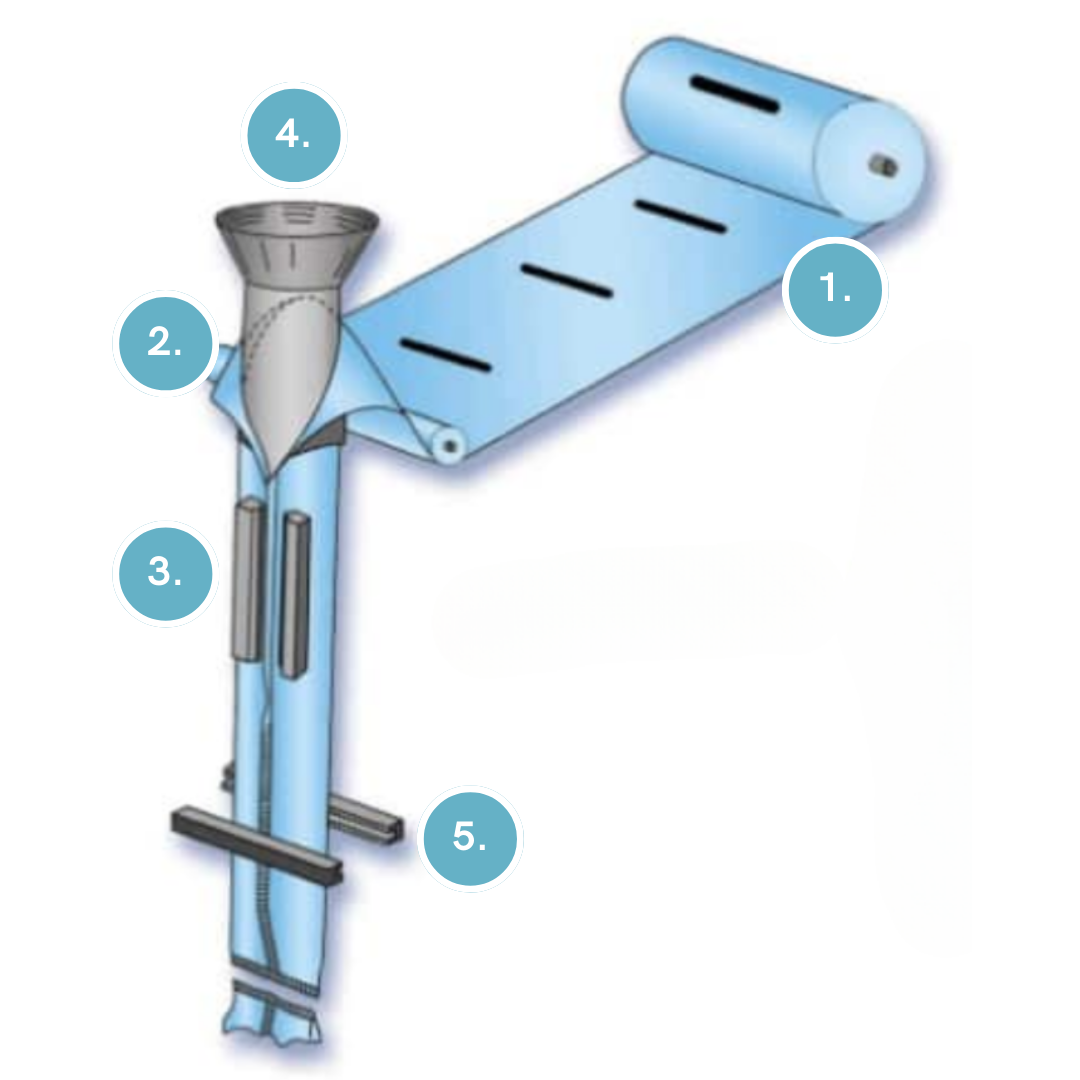
Step-by-Step Process of Rollstock Packaging
- Unwinding – The rollstock material is unwound from a spool.
- Forming the Pouch – The film is shaped into a pouch using various folding techniques.
- Sealing – Heat, pressure, or ultrasonic sealing fuses the pouch edges.
- Filling – The product is dispensed into the formed pouch.
- Final Sealing & Cutting – The pouch is sealed shut and cut from the roll, ready for distribution.
Types of Machines
-
1. Vertical Form-Fill-Seal (VFFS) Machines
- Film moves vertically through the machine.
- Pouches are formed around a tube, sealed along the back, filled from the top, and then sealed at the bottom.
- Common pouch styles: Pillow pouches, gusseted bags, stick packs.
-
2. Horizontal Form-Fill-Seal (HFFS) Machines
- Film moves horizontally through the machine.
- Pouches are formed, filled, and sealed in a single pass.
- Common pouch styles: Stand-up pouches, 3-side seal pouches, flat pouches.
Pouch Formats from Rollstock
Rollstock pouches can be formed into just about any pouch shape you can get as standalone pouch, it just takes the right equipment. This includes:
-
Flat Sachets / 3-Side Seal Pouches
- Most common, simple, cost-effective
- Great for single-serve items, powders, liquids
- Most common, simple, cost-effective
-
Stand-Up Pouches (SUPs)
- With bottom gussets (Doy-style)
- Can include zippers, valves, or spouts (with added steps)
- With bottom gussets (Doy-style)
-
Pillow Pouches
- Often used for snacks, coffee, or powders
- Sealed at top and bottom with a vertical back seal
-
Stick Packs
- Long, narrow single-serve pouches (think energy powders, supplements)
- Vertical FFS machinery forms and seals these from rollstock
-
Spouted Pouches
- Can be formed from rollstock with specialized machinery
- Spout insertion is usually a separate step after forming/filling
-
Flat Bottom Pouches
- Square shape, with side gussets and flat bottom
- Requires more advanced horizontal form-fill-seal equipment
- Best for high-end food products or when shelf presence matters
-
Gusseted Side-Seal Bags
- Often used for larger volume dry goods (grains, pet food)
- Rollstock forms the pouch with expandable side gussets
Industries That Benefit from Rollstock Packaging
Rollstock is widely used in industries requiring high-speed, high-volume packaging, some examples include:
-
Food
Snack pouches, coffee bags, protein powders
-
Pet Food
Dry food pouches, treat bags and stick packs
-
Cosmetics
Face masks, sample sachets
-
Cannabis
Child-resistant packaging for edibles and supplements
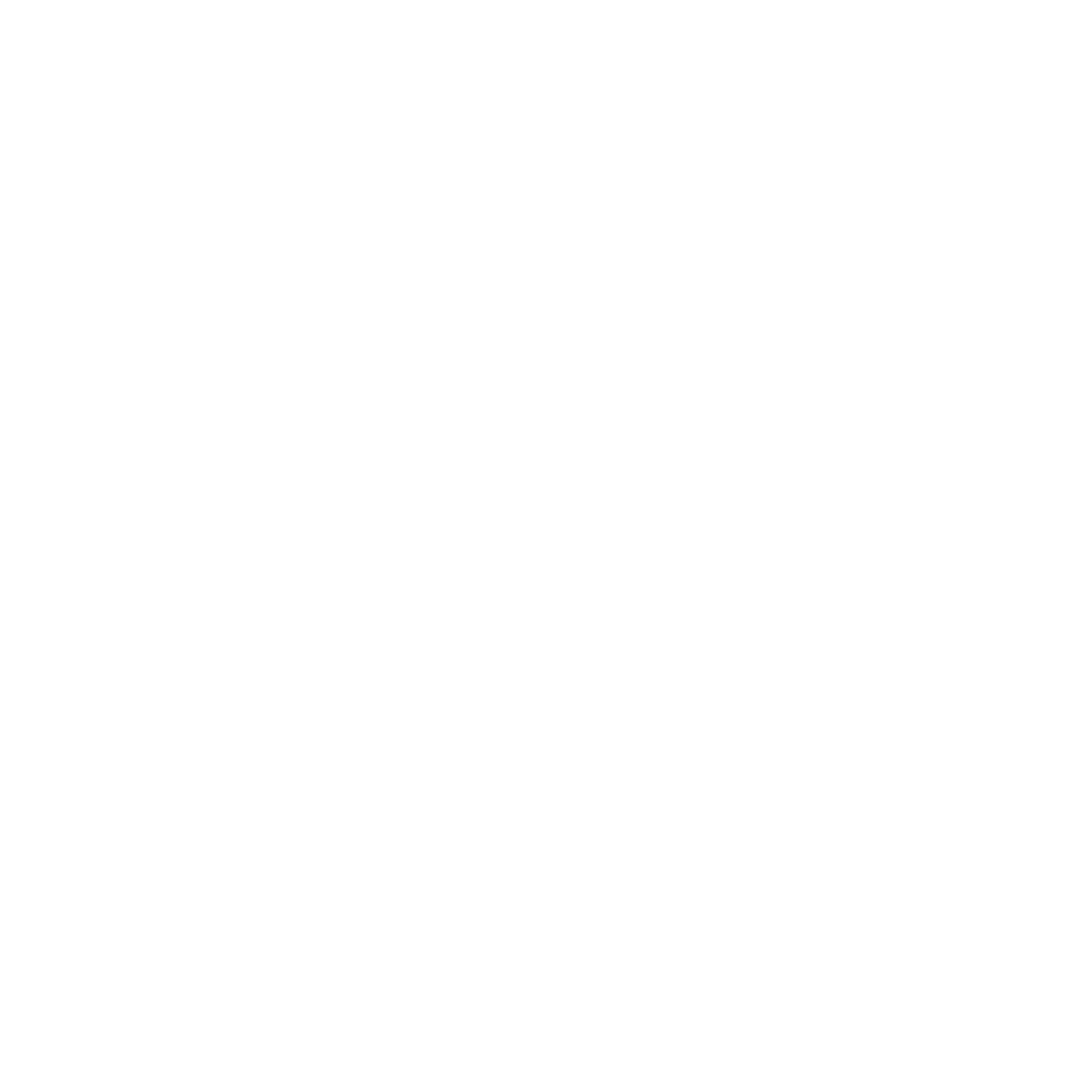
How Much Volume Justifies Rollstock?
For businesses packaging at least 50,000 to 100,000 units per month, rollstock packaging offers substantial savings in material costs and labor efficiency. Companies handling hundreds of thousands to millions of pouches per month can achieve even greater benefits from this automation.
Sealing Methods in Rollstock Packaging
Sealing ensures pouch integrity, product freshness, and barrier properties. The method depends on material type, product sensitivity, and production speed.
-
1. Heat Sealing (Thermal Sealing)
Uses heated jaws to melt and bond the sealant layer.
Common for: Food, pet food, pharmaceuticals, and cosmetics.
Pros: Strong seals, reliable for high-speed production.
Cons: Can cause shrinkage in heat-sensitive films.
-
2. Ultrasonic Sealing
Uses high-frequency vibrations to melt the sealant only at the seal area.
Best for: Heat-sensitive materials, liquid or powder products that may contaminate seals.
Pros: Seals through contaminants, lower energy consumption.
Cons: Expensive machinery, not compatible with all films.
-
3. Cold Sealing (Pressure Sealing)
Uses pressure to bond pre-applied adhesive without heat.
Best for: Heat-sensitive products like chocolate and pharmaceuticals.
Pros: No heat required, very fast sealing.
Cons: Requires special cold-seal films, weaker than heat or ultrasonic seals.
Material Options, Barrier Considerations & Customization
Selecting the right material for rollstock packaging is essential to achieving the necessary product protection while remaining as eco-friendly as possible. Available material options include:
-
Relaminate™
Standard multi-layer laminate for durability and strength.
-
Biolaminate™
Environmentally friendly option with sustainable components.
-
C20 Compostable Laminate
Fully compostable film for eco-conscious brands.
Additionally, rollstock packaging supports the same barrier properties available in other pouch types, including oxygen, moisture and UV barriers.
Customizable features
-
Windows
Allows consumers to see the product inside
-
Zippers
Resealable closures for multi-use convenience
-
Spouts
Ideal for liquid-based product
-
Laser Scoring
Enables easy opening without tearing the packaging unevenly.
Is Rollstock Right for You?
-
If you're working with a third-party packager or co-manufacturer, the first step is understanding the equipment they use. Rollstock requires specific forming and sealing machinery, so your packaging must be tailored to match their capabilities for a proper fit, reliable seal strength, and optimal performance.
-
For growing brands, rollstock offers major advantages:
- Lower per-unit costs with less material waste
- High-speed production ideal for scaling
- Customization options like zippers, spouts, and valves
- Enhanced product protection with high-barrier materials
Not sure where to start? We’ll help you.